What should you be considering when planning cleanroom cleaning after a renovation? Micronclean’s Business Development Manager David Giles explains
There are many reasons why a cleanroom may require renovation, from replacing floors to ventilation and filtration systems, either way, the cleanroom will need some attention in order to make it fit for operation again.
Due to the disruption to the cleanroom and the inevitable addition of particulate and microbiological contamination, cleaning is a critical aspect of this process.
In a way, the cleaning processes following a renovation will be very similar to that of a new cleanroom build. In both scenarios, there are certain considerations when planning cleanroom cleaning which include:
What is the measure of success?
You first need to decide how ‘clean’ the cleanroom needs to be in order to be fit for operation. Whilst many people will worry about not doing enough cleaning, it can be just as easy to do more than is required. Rather than simply doing ‘what has always been done’ or ‘how it was done at a previous organisation’, time should be taken to assess what needs doing and the level of cleanliness that is required.
Some of the reagents you will need could include Neutral Detergent, WFI, IPA/denatured ethanol, biocide/sporicide
Once an assessment of the required cleanliness has been completed, you need to consider how you will be defining ‘clean’. Depending on the cleanroom classification you are operating in, this might include limits for visible contamination, particulate contamination and microbiological contamination. In addition to clarifying how ‘clean’ will be defined, consideration should be given to how the cleanliness will be measured. There are a number of questions to ask yourself, for example, is physical and/or microbiological environmental monitoring required? If this is the case, do you have an adequate routine in place? You may also consider if a thorough survey is required.
How will the required level of cleanliness be achieved?
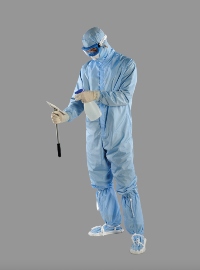
Identifying what needs to be cleaned is the best place to start. You will need to consider floors, walls and ceilings, as well as inside and outside equipment, and any high-level cleaning or other specialist cleaning that may be required.
The next step in the process should be to understand what contamination is likely to be present after the renovation. There is likely to be significant physical contamination (e.g. dust and sealants), but you should also consider microbiological contamination such as spores.
Once you have clarity on what needs to be cleaned, you are ready to consider how the cleaning will take place. For example, does the cleaning need to be phased? Dependent on the cleanroom and its renovation, it may be best practice to phase the cleaning process into the following processes:
- Cleaning of gross contamination prior to HVAC system being turned on
- Cleaning before equipment is positioned and installed in the cleanroom
- Fine cleaning once HVAC system is in operation
The method of cleaning is vital in the process in order to ensure compliance when commencing work in the newly renovated cleanroom. You will need to ensure the cleaning methods are GMP compliant and follow best practice recommendations. It is also worth checking if the chosen cleaning processes have been validated or proven to be effective in any way.
The selection of materials and equipment should always refer to the point made earlier in the article about identifying what you are aiming to achieve from the clean. Asking yourself again if the clean needs to follow full GMP best practice methods and then deciding what will be required from there.
Like any project, timelines can slip with little to no notice
Some of the reagents you will need could include Neutral Detergent, WFI, IPA/denatured ethanol, biocide/sporicide, but even once you have made the selection, there are some questions to ask yourself. Have the products been validated for use? Are the reagents compatible with one another and are they compliant? Once you have determined if the products are validated, compatible and compliant, you should ensure stable supply for the required quantity and period. This will require you to know how much stock you need for the cleaning and have an approved supplier for the items.
Reagents play a huge role in getting your cleanroom clean. However, you will also need to consider the equipment you use to clean, apply products and remove residues. Common equipment used for cleaning cleanrooms include vacuums, mops, wipes, sprays and fogging, to name a few. Additional equipment may be required for hard-to-reach areas of the cleanroom, including high level access equipment and safety equipment, etc.
How will the cleaning be completed?
Personnel and resource are two key areas to consider when thinking about how cleaning will be completed after a cleanroom renovation. It is important to ensure the team who will be carrying out the cleaning are suitably trained and experienced, to ensure good practice is adhered to. Whether you clean using your own staff or have a professional cleanroom cleaning partner, the operators should be trained and familiar with all aspects of cleanroom gowning, material transfer, GDP and GMP. This includes GMP cleaning as well as the equipment and materials that they will be using throughout the process.
You need to consider how you will be defining ‘clean’
By ensuring you have allocated sufficient time and resource for cleaning after a renovation, you increase your ability to complete the project on time and to the correct level of quality. Like any project, timelines can slip with little to no notice. With this in mind, it may be worth allowing a contingency within the plan or considering if the resource is flexible enough to meet a revised deadline.
Specific PPE and training may be required for all personnel. All safety considerations should be made before commencing the clean and planned into the project schedule.
Once the cleanroom is clean, how will cleanliness be maintained?
Now that the deep clean is completed and you have a newly renovated cleanroom, you have a responsibility to maintain the cleanliness. Many organisations use specialist cleanroom cleaning companies to support the design and fulfilment of effective and efficient cleaning, starting with a deep clean and then leading into routine cleans.
The benefits of using a professional cleanroom cleaning service is their expertise built through specialisation, thorough training and experience. The quality of the clean is always consistent, with full documentation and traceability to support this. A cleanroom cleaning specialist will also take responsibility for cleaning equipment and consumables stock through their established supply chains and can be flexible around clients’ deadlines and time constraints.
Next time you are building a cleanroom or having a renovation done, it will serve you well to start at the beginning and plan cleaning as a critical aspect of the overall programme. Alternatively, you can outsource this service and rely on the work of professionals.